Nie tylko dla automotive
Od 2012 roku w sandomierskim zakładzie jednego z największych producentów szkła na świecie zaczęto wprowadzać World Class Manufacturing. Wyniki osiągnięte po tym czasie są więcej niż zadowalające, co może stanowić potwierdzenie dla firm farmaceutycznych, że filozofi a ta sprawdza się nie tylko w automotive.
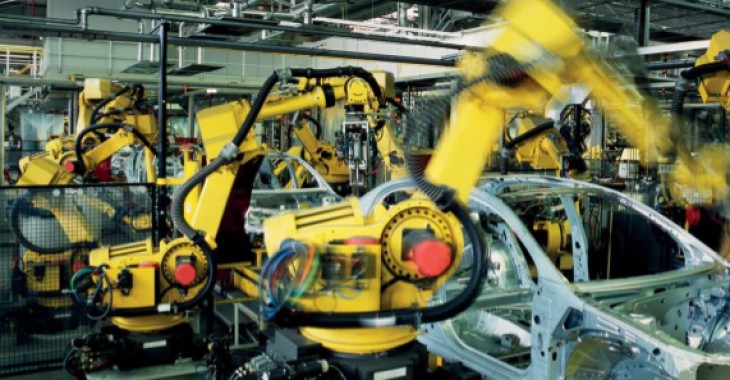
Pilkington Automotive Poland jest częścią Nippon Sheet Glass (NSG). Grupa ta jest jednym z największych producentów szkła na świecie – mamy ok. 25% udziału w rynku. Specjalizujemy się w szkle płaskim, samochodowym oraz technicznym. W Polsce nasze zakłady znajdują się w Sandomierzu i Chmielowie, gdzie wytwarzamy dla branży automotive – co 10 szyba montowana w samochodzie w Europie pochodzi od nas.
Organizacja ciągle się rozwija. Największe inwestycje miały miejsce w latach: 1998 – budowa zakładu w Sandomierzu, 2004 – rozbudowa zakładu w Sandomierzu, 2012 – budowa zakładu w Chmielowie, 2015 – rozbudowa zakładu w Chmielowie.
Inwestujemy także w rozwój strukturalny. Od 2012 roku w kooperacji z Fiat Auto Poland, który jest jednym z naszych klientów, wprowadzamy w sandomierskim zakładzie World Class Manufacturing (WCM). Wyniki, jakie osiągnęliśmy po tym czasie, są więcej niż zadowalające. Nic jednak nie przyszło od razu. Na początku WCM uzmysłowił nam konieczność przeanalizowania skuteczności naszego działania. Identyfi kacja poniższych problemów pozwoliła jednak zrobić kolejne kroki do przodu.
Wewnętrzna konkurencja
Linie produkcyjne, choć w większości zintegrowane, były podzielone na węzły. Zarządzali nimi na zmianach pierwsi operatorzy, a za całość węzła odpowiadał lider pracujący na dziennej zmianie. Trzy węzły tworzyły jedną linię produkcyjną zarządzaną przez kierownika wydziału. Wraz ze wzrostem świadomości naszych operatorów co do kosztów strat, wprowadzania celów węzłowych oraz oceny pracy poszczególnych węzłów, zaobserwowaliśmy wewnętrzną konkurencję. Była ona szczególnie problematyczna przy dzieleniu zasobów pomiędzy węzłami, przy zarządzaniu jakością danych w systemie SAP, a także przy zachowaniu dyscypliny w porze nocnej.
Silosowa hierarchia i paradoks spotkań
Wydziały produkcyjne są wspierane przez służby jakościowe, logistyczne, utrzymania ruchu i oprzyrządowania. Zaobserwowaliśmy problemy w komunikacji oraz podejmowaniu decyzji. Często bywało tak, że decyzja musiała przejść przez „silosową hierarchię” – musieli ją podejmować dyrektor produkcji np. z dyrektorem technicznym po uprzednim przeanalizowaniu (oczywiście po raz kolejny) tych samych danych wejściowych. Problemy z komunikacją uwidoczniły się w paradoksie spotkań – każdy twierdził, że spotkań jest za dużo, ale do podjęcia decyzji potrzebne były kolejne.
Wiele podobnych stanowisk
Na każdym wydziale produkcyjnym zwyczajowo pracowało trzech technologów w wąskich specjalizacjach. W trakcie rozbudowy zakładu o kolejne linie produkcyjne, musieliśmy tworzyć bardzo podobne stanowiska, gdyż główny ciąg technologiczny dla szkła samochodowego jest w miarę standardowy.
Utrudniony przepływ informacji
WCM opiera się na 10 filarach technicznych – w naszym zakładzie dyrektor ds. jakości jest liderem
wdrożenia WCM, zaś liderami fi larów są kierownicy i specjaliści wspierani przez swoich funkcjonalnych przełożonych w randze dyrektorów poszczególnych pionów. Co ciekawe, typowa produkcja jest stricte odzwierciedlona w fi larze WO (workplace organization). W trakcie jej wdrażania zaobserwowaliśmy kolejny problem związany z przepływem informacji – liderzy fi larów mieli kłopot z sformowaniem zespołów roboczych na poszczególnych linach produkcyjnych.
Zmiana struktury organizacyjnej
Aby rozwiązać wymienione problemy, zdecydowaliśmy się na zmianę naszej struktury organizacyjnej:
- lider zmiany produkcyjnej – zamiast liderów węzłów (3 x wydział, zmiana dzienna) wprowadziliśmy liderów zmiany produkcyjnej, pracujących na 3 zmianach, odpowiadających za cały wydział, raportujących do kierownika wydziału;
- Natural Working Group (NWG) – wszyscy specjaliści z działów wspomagających produkcję (jakości, logistyki, utrzymania ruchu oraz oprzyrządowania), zostali „geografi cznie” przeniesieni do biur na wydziałach produkcyjnych, natomiast organizacyjnie raportują linią przerywaną do kierownika wydziału produkcyjnego; jednocześnie każdy z członków NWG ma konkretne zadania w poszczególnych fi larach WCM;
- zespół technologiczny – na liniach produkcyjnych zostawiliśmy po jednym technologu, natomiast pozostali stworzyli zespół specjalistów obsługujący wszystkie wydziały produkcyjne, zajmując się standaryzacją procesów produkcyjnych, rozwijaniem nowych technologii oraz nowych modeli.
Cele efektywnościowe
Skuteczność zmian strukturalnych określamy m.in. wynikami wdrożenia projektu WCM. Każdy wydział produkcyjny otrzymał cele dotyczące poprawy efektywności w oparciu o stratyfi kację strat wg fi laru CD, wskaźniki dotyczące BHP (Safety), ilości projektów i wdrażania narzędzi do rozwiązywania problemów (FI), awaryjności (AM & PM), produktywności (WO), kosztów i jakości (QC), dystrybucji wiedzy oraz kosztów szkoleń (PD). Dodatkowo wszyscy pracownicy zgłaszają pomysły us prawniające, które mogą przekształcić się w projekty KAIZEN w wyniku działań zespołu NWG.
Uzyskane rezultaty
Wyniki tych wszystkich zmian są bardzo ciekawe – poziom oszczędności sięga 8% kosztów rok do roku przy realizacji ponad 1600 projektów KAIZEN. Wprowadzenie powyższych działań pozwoliło również na obsadzenie stanowisk funkcyjnych na nowo powstałych liniach, wykorzystując obecne zasoby. Projekt został bardzo wysoko oceniony przez zespół zarządzający Grupy NSG, stając się wyznacznikiem kierunku dla pozostałych zakładów.
Cały artykuł można przeczytać w numerze 4-5/2015 magazyn "Przemysł Farmaceutyczny"
Fot. www.photogenica.pl