Bierze problemy „na stół” - wywiad z Andrzejem Urlińskim
– Pomysły i inspiracje dają nam nasi klienci. Rozwiązań nie wymyślamy na zawołanie, ale „na stół” bierzemy realne problemy techniczne, jak i technologiczne kontrahentów, zastanawiając się, jakie usprawnienia zastosować – mówi Andrzej Urliński, właściciel Zakładu Usług Technicznych.
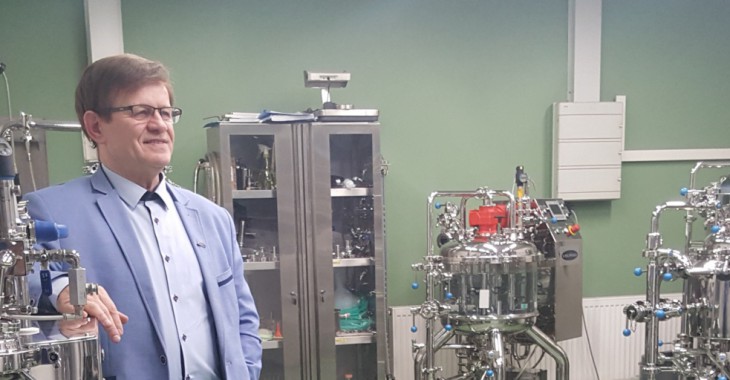
Podczas debaty zorganizowanej w trakcie XIII Jesiennego sympozjum Przemysłu Farmaceutycznego i Kosmetycznego zastanawialiśmy się nad tym, czy zakłady farmaceutyczne i kosmetyczne w Polsce są nowoczesne. Są?
Jeżeli chodzi o firmy farmaceutyczne w naszym kraju, to znam szereg zakładów, które rzeczywiście rozwijają się w bardzo szybkim tempie, co zauważam podczas spotkań u moich klientów. Nie odbiegają, a wręcz w niektórych przypadkach wyprzedzają spółki farmaceutyczne w Europie. Wprawdzie unowocześnianie zakładu wiąże się z dużymi i kosztownymi inwestycjami, ale nasi, często młodzi technolodzy, którzy jeszcze całkiem niedawno byli studentami, dziś wdrażają innowacyjne rozwiązania w swoich zakładach naprawdę dobrze – od działu R&D aż po produkcję. Cieszymy się, że możemy to robić wspólnie z nimi, pomagając w realizacji ich pomysłów. Głównie mam tu na myśli stosowane technologie w formach mokrych, w których się specjalizujemy. Na konferencji BMP spotkałem wielu dobrych, znających się na swoim fachu młodych specjalistów. Usłyszałem też, kiedy ktoś instruował technologa, pokazując rozwiązania jeszcze z XX wieku – rozśmieszyło mnie to, ponieważ tych ludzi nie trzeba dziś pouczać, a pokazywać rozwiązania nowocześniejsze, dając im pole do rozwoju.
Podczas prezentacji przedstawił pan wasz nowy produkt.
Przez wiele lat byłem pytany o to, kiedy zrobimy urządzenie laboratoryjne mniejsze niż 5 litrów. Dziś mamy już sprawdzony w działaniu mieszalnik laboratoryjny o poj. max 2 l oraz 0,6 l pojemności minimalnej, a to wszystko dzięki naszym klientom, którzy podkreślali, że te 5 l to za dużo. I od teraz mamy wdrożone rozwiązanie typowe w scale-up – z mniejszej na wyższą, zgodnie z normami FDA. Jest to urządzenie kompletne i kompaktowe, które posiada w sobie wszystkie narzędzia, jak mieszanie, homogenizacja bay-pass, chłodzenie, próżnia itp... Nie ma więc potrzeby kompletowania narzędzi w zależności od wymagań. Omawiane urządzenie posiada wszystko, co może się przydać technologowi podczas wrażania nowej formuły kosmetycznej czy też farmaceutycznej. Tak zaawansowane technologicznie rozwiązanie w tak małej skali w Polsce proponujemy tylko my i jedna firma z Niemiec.
Czy w pana planach na przyszłość są nowe inwestycje?
Jeśli starczy zdrowia, to pomysłów mam jeszcze wiele. Chciałbym się np. zająć granulacją – temat ten z pewnością byłby dla mnie wyzwaniem i mamy już gotową dokumentację koncepcyjną. Pomysły i inspiracje dają nam nasi klienci. Rozwiązań nie wymyślamy na zawołanie, ale „na stół” bierzemy realne potrzeby, jak i problemy naszych kontrahentów, zastanawiając się, jakie usprawnienia zastosować. Jako przykład mogę podać jedną z firm farmaceutycznych, która chciała wytworzyć dwa różne produkty. Okazało się, że powinny powstawać na dwóch odrębnych urządzeniach. Po pierwszych testach w laboratorium firma ta stwierdziła, że decyzja, którą z maszyn wybrać do swojego zakładu, jest bardzo trudna, ponieważ mają miejsce tylko na jedno stanowisko produkcyjne. Zaintrygowało mnie to na tyle, że po trzech dniach pojechałem do ich fabryki z gotowym rozwiązaniem, żeby zaproponować rozwiązanie typu 2w1 – tak zresztą je nazwaliśmy. Klient oczywiście docenił nasz wysiłek oraz inicjatywę i zamówił to rozwiązanie, które od ponad 2 lat sprawuje się doskonale. Od tamtej pory produkujemy tę maszynę prawie wyłącznie w tej formie.
Na czym polega to rozwiązanie?
Na odcięciu specjalnym zamknięciem komory homogenizatora, co daje możliwość korzystania z homogenizatora, bądź nie. To rozwiązanie daje wręcz niegraniczone możliwości technologiczne wykorzystania mieszalnika do bardzo wielu zadań procesowych i zastępuje często mieszalniki zadaniowe dla przygotowania faz. Obecnie klienci praktycznie zawsze wybierają urządzenia posiadające tę funkcję, a mają w czym wybierać, gdyż dziś mamy do dyspozycji klientów cały typoszereg urządzeń procesowych: od 2 aż do 5000 litrów, oczywiście wg zasad scale-up, zgodnych z normami FDA.
Wracając do tematu nowoczesnych zakładów. Jakie wg pana są wyznaczniki tego, że firma jest nowoczesna?
Moim zdaniem nowoczesna firma, która produkuje np. kosmetyki czy też farmaceutyki, powinna starać się, aby produkt był optymalny. Oznacza to wykorzystanie wszystkiego, co bierze udział w procesie. Wyrób musi być jednorodny, powtarzalny, stabilny. Najważniejsze jest, aby cały proces tworzenia produktu był kontrolowany przez odpowiednie czujniki oraz archiwizowany zgodnie z zasadami GMP. To bardzo istotne, aby zagwarantować, że wyrób będzie najwyższej jakości, odpowiadający wymogom dyrektywy kosmetycznej czy farmakopei. Kontrole jakości – większość przedsiębiorstw je posiada, ale przypominam sobie jeszcze lata, gdy uruchamiałem firmę Soraya w Radzyminie. Stworzyliśmy wtedy archiwum gotowych produktów, które bardzo się przydało. Jakiś czas później pojawił się u nas bowiem sanepid i dzięki temu, że posiadaliśmy wspomniane archiwum, byliśmy w stanie udowodnić, że jedna z reklamacji była nieuczciwym zagraniem pewnej osoby, która chciała uzyskać określone korzyści. Ten sam produkt, tej samej serii oddaliśmy do badania w sanepidzie i okazało się, że klientka kupiła wyrób kosmetopodobny, w oryginalnie wyglądającym słoiku, produkowanym wówczas zapewne na potrzeby jarmarku na Stadionie X-lecia w jakimś garażu – uczulił ją po prostu któryś z surowców. Wyszliśmy ze sprawy obronną ręką.
Do czego służy to przezroczyste urządzenie, które zademonstrował pan podczas konferencji?
Działam w branży od ponad 30 lat. Współpracuję ze studentami, prowadzę dla nich warsztaty. Po zajęciach teoretycznych schodzimy do mojego laboratorium badawczego i pokazuję, jak urządzenie wygląda, na jakich zasadach działa, bo tylko tak widać wszystkie elementy technologiczne w pracy i ich działanie procesowe. Po to, aby zajęcia były jak najbardziej przydatne i urozmaicone, wykonujemy jedną z form emulsji kosmetycznej.
Urządzenie, które przywiozłem ze sobą na sympozjum, jest przezroczyste właśnie po to, aby również inni technolodzy mieli możliwość szybciej zrozumieć zastosowane rozwiązania technologiczne i zobaczyć cały wewnętrzny mechanizm wykorzystanych narządzi, których normalnie nie widać, gdyż urządzenie jest w wersji produkcyjnej wykonane ze stali kwasoodpornej i oczywiście nietransparentnej. Nie muszę apelować do ich wyobraźni, tylko pokazuję zasadę działania i zachodzące procesy technologiczne.
Mamy też takie samo przezroczyste urządzenie dla przemysłu farmaceutycznego – typowo dla sterylnych produktów infuzyjnych, kropli do oczu, kropli do nosa, kropli do uszu itp. Dzielę się wiedzą z młodymi ludźmi, by mogli kontynuować moje dzieło, żeby poznali rozwiązania nie z XX, ale z XXI wieku, kiedy wszystko zmienia się w szalonym tempie. Kiedyś miałem kilku klientów. Dziś mam ich ponad 200 z całego świata. To firmy małe, rodzinne, ale i spółki, koncerny z pierwszych stron gazet. Przez lata zdobyłem we współpracy z nimi szereg doświadczeń, którymi dziś chcę się dzielić z moimi klientami i podtrzymywać zaufanie, jakim obdarzyli moją firmę.
Rozmawiała: Agata Paszek
Wywiad ukazał się w dwumiesięczniku "Przemysł Farmaceutyczny" 6/2017.
Komentarze