Centralne usuwanie pyłów chroni przed kontaminacją. Renowacja urządzeń zwiększa bezpieczeństwo
W zakładzie firmy Cilag w Schaffhausen produkowane są różnego rodzaju leki farmaceutyczne. Odpylanie urządzeń produkcyjnych odbywa się za pomocą sześciu dwustopniowych filtrów. Zebrany pył usuwany jest poprzez 27 szt. pojedynczych zbiorników na pył z plastikowym workiem. Takie proste pozbywanie się pyłów przestało spełniać wymogi stawiane produkcji wolnej od zanieczyszczeń i zostało zastąpione przez centralne usuwanie pyłów.
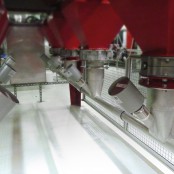
Cilag w Schaffhausen to jeden z największych producentów przemysłu farmaceutycznego w Szwajcarii, należący do koncernu Johnson & Johnson. Aby móc stale stosować najnowocześniejsze i ekonomiczne technologie i procesy, konieczna jest systematyczna kontrola urządzeń pod kątem ich bezpieczeństwa i ekonomiczności. W odniesieniu do odpylania produkcji pomiar stanu faktycznego w 2008 roku wykazał, że pięć dwustopniowych filtrów zawiesin koloidalnych nie jest w stanie już sprostać wysokim wymaganiom. Wprawdzie same filtry i ich stopień filtracji w dalszym ciągu odpowiadał najwyższym wymogom, ale problem polegał na usuwaniu pyłów. Technologia nie spełniała już wymagań stawianych produkcji wolnej od zanieczyszczeń, a wymiana plastikowych worków była zbyt czasochłonna. Dodatkowo wymiana pełnych worków możliwa była wyłącznie w pełnym kombinezonie ochronnym.
Nadszedł zatem czas na renowację instalacji. W praktyce oznaczało to spełnienie rozmaitych wymagań postawionych. Po pierwsze, oczekiwano stworzenia tylko jednego jedynego punktu odbioru pyłu, a transport i usuwanie pyłu miały odbywać się bez narażenia na kontaminację. Przewidziano wysokie standardy bezpieczeństwa w obudowie bezpieczeństwa (containment), długie przerwy między wymianami i 24 godzinny okres eksploatacji przez 5 do 7 dni w tygodniu. Jednocześnie nie wolno było dokonywać żadnych (technicznych) modyfikacji w istniejących aparatach DES.
Aby zrealizować te wymagania, Herding zastąpił zbiorniki na pył pneumatycznym transportem zebranych pyłów do centralnego separatora. Separator uzbrojony jest w system CLS (Continuous Liner System), który umożliwia wydalanie pyłu bez zagrożenia zanieczyszczeniem. Pyły umieszczane są teraz w zgrzewanych workach plastikowych umożliwiających wygodną utylizację. Żywotność elementów filtrujących w centralnym odsysaniu wynosi min. 5 lat. Do podłączenia przewodów ssących do poszczególnych śluz istniejących filtrów Herding skonstruował specjalne końcówki odsysające, połączone z kolei z głównym przewodem ssącym. Dzięki tym działaniom powstał zamknięty i bezpieczny system.
Obecnie dziewięć kanałów przewodu rurowego zbiega się na wysokości pierwszego stopnia filtracji centralnego odpylacza. Pierwszy stopień filtracji jest wyposażony w filtry z wkładami ze spiekanego polietylenu. Charakteryzują się one stopniem filtracji do poziomu <0,2 mg/m3 oraz długą żywotnością, zatem obudowa filtra wymaga otwarcia dopiero po latach. Drugi poziom filtracji składa się z jednego filtra HEPA o klasie sprawności H14, którego kasetę filtrującą można usunąć bez narażania na skażenie znaną metodą bag-in-bag-out. Okresy wymiany są odpowiednio długie ze względu na stałą i wysoką skuteczność filtracji.
Obudowa chroni pracowników
Wydalanie pyłów do CLS odbywa się również bez ryzyka kontaminacji. Decydując się na inwestycję, klient wybrał rozwiązanie ze zgrzewaniem worków foliowych.
Do kolektora pyłów podłączony jest za śluzą pakiet węży foliowych, dzięki czemu zebrany pył trafia bezpośrednio do plastikowego węża. Poniżej znajduje się zgrzewarka z trzema szczękami rozmieszczonymi jedna nad drugą. Dolna szczęka zamyka worek, środkowa wykonuje spaw zabezpieczający i odcina foliowy wąż, a trzecia szczęka zamyka foliowy wąż jako dno dla następnego worka. Zamknięty kartonowy pojemnik z workiem można teraz bezpiecznie usunąć, a kolejny worek foliowy opuścić do nowego pojemnika kartonowego. Ilość wydalonego pyłu to ok. 80 l. Dodatkowo punkt odbioru pyłu podłączony jest osobnym kanałem z instalacją filtrującą, utrzymującą stałe podciśnienie. Dzięki takiemu rozwiązaniu możliwe było spełnienie wysokich wymagań containment (OEL <1 μg/m3) także w razie awarii.
Sterowanie instalacją
Należy też wspomnieć o systemie sterowania całą instalacją, którego centralnym elementem jest sterownik PLC z terminalem obsługi. Rejestruje on sygnały istniejących instalacji DES łącznie z wydalaniem pyłu, steruje zaworami w poszczególnych przewodach ssących i przetwarza sygnały czujników ciśnienia (podciśnienie w przewodach ssących, różnica ciśnień na obu stopniach filtracji). Poza tym sterownik PLC steruje wydalaniem pyłów i rejestruje ciężar pojemnika z pyłem przeznaczonym do utylizacji.
W połączeniu ze sterownikiem PLC pracuje sterownik MP12 firmy Herding. Nadzoruje on pracę filtrów, rejestruje dane logowania, dysponując pamięcią wewnętrzną do maks. 2000 wpisów.
Modernizacja rozwiązań produkcyjnych ma ogromną korzyść dla użytkowników: przestrzeń produkcyjna wolna jest od zanieczyszczeń – bardzo wysoki stopień ochrony pracowników. Dzięki długim okresom eksploatacji filtrów zredukowano czasy przestojów oraz zaoszczędzono koszty konserwacji i części zamiennych. Usuwanie pyłów odbywa się tylko raz na 3-4 dni i jest teraz na tyle bezpieczne, że pracownicy nie potrzebują zakładać pełnego kombinezonu ochronnego. Pomieszczenie techniczne, zaklasyfikowane wcześniej do specjalnego poziomu bezpieczeństwa, jest obecnie normalnym pomieszczeniem technicznym, dostępnym bez jakiegokolwiek sprzętu ochrony osobistej, co ułatwia także konserwację pozostałych agregatów i urządzeń znajdujących się w tym pomieszczeniu.
Podsumowując, trzeba podkreślić, że rozwiązania te sprawdzają się już od ponad 2 lat, a w międzyczasie instalacja Herding została uzupełniona o odbiór pyłów z dwóch kolejnych filtrów Stefan Kollischan, Project Engineer HVAC & Maintenance w Cilag, wyjaśnia: „Modernizacja i rozwój dokonany przez Herding Filtertechnik umożliwił nam dalsze wykorzystywanie istniejących urządzeń i jednoczesne spełnienie naszych wysokich wymagań odnośnie ochrony ludzi i maszyn przed pyłami o dużej aktywności. Jednocześnie udało się na tyle zredukować nakłady i koszty, że inwestycja zamortyzowała się już po 1 roku.”
www.herding.pl
Autor: dr inż. Hans-Joachim Adlhoch
Artykuł sponsorowany został opublikowany w magazynie "Przemysł Farmaceutyczny" nr 1/2012